Ensuring Operational Excellence: The Importance of PLC Maintenance
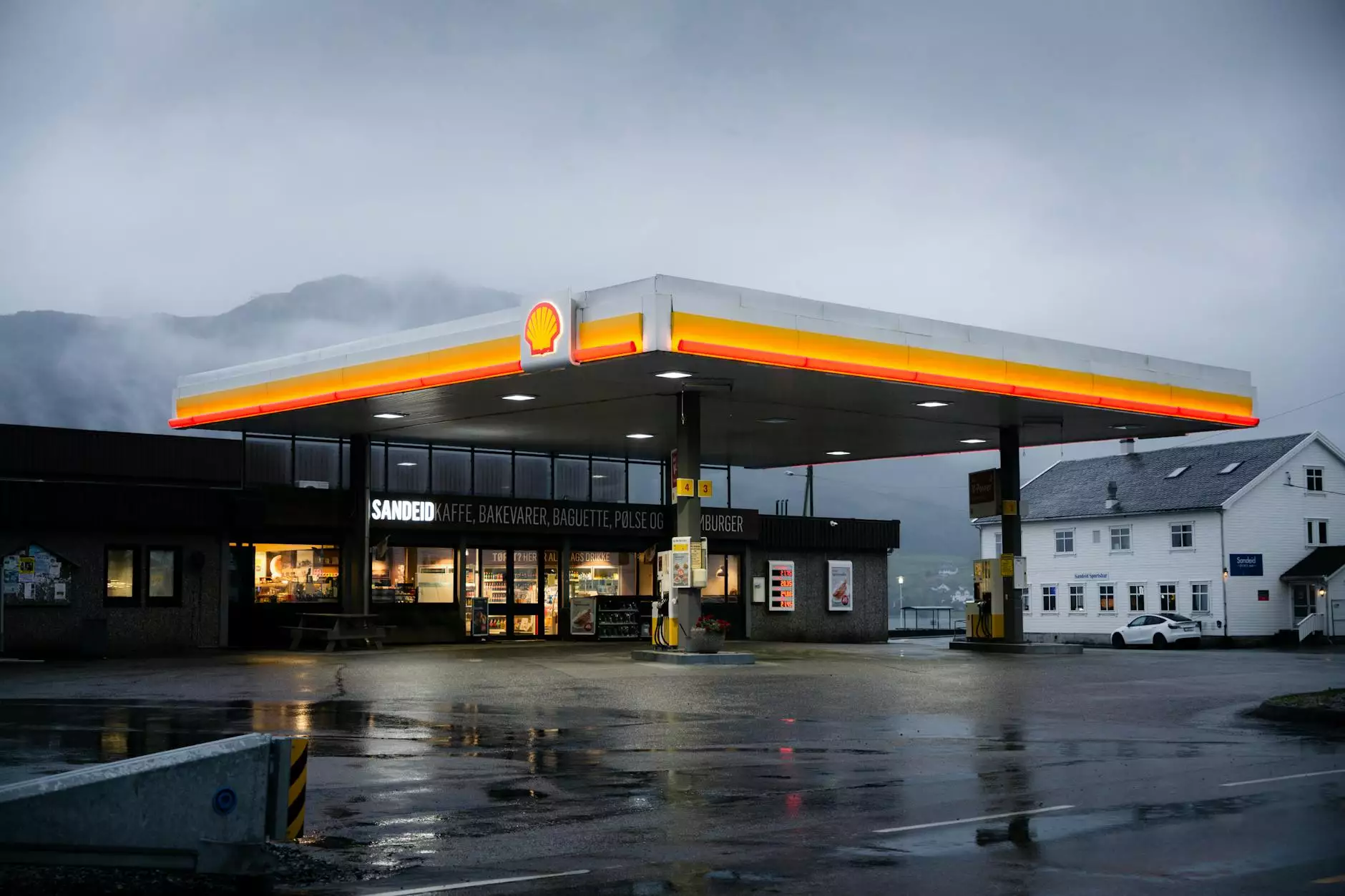
Programmable Logic Controllers (PLCs) serve as the backbone of many industrial operations and automation processes. Their reliability and functionality are crucial in various sectors, including manufacturing, energy production, and logistics. In this comprehensive guide, we delve into the significance of PLC maintenance, the benefits of partnering with a trusted electronic components distributor in Canada, and the value of professional PLC repair services.
What Is PLC Maintenance?
PLC maintenance comprises all activities designed to ensure a programmable logic controller functions correctly throughout its lifecycle. This includes regular inspections, software updates, hardware checks, and proactive troubleshooting. Implementing an effective maintenance program is vital for:
- Reducing Downtime: Regular maintenance helps identify and fix potential issues before they lead to unexpected breakdowns.
- Extending Equipment Life: Taking care of your PLCs prolongs their operational lifespan, providing a better return on investment.
- Enhancing Safety: Proper maintenance reduces the risk of accidents associated with equipment failure.
- Improving Efficiency: Well-maintained PLCs operate at optimal performance, contributing to smoother production processes.
Types of PLC Maintenance
PLC maintenance can be categorized into two main types:
1. Preventive Maintenance
Preventive maintenance involves scheduled checks and activities that aim to prevent malfunctions. Key tasks include:
- Regular inspection of connections and cables
- Software updates to improve functionality and security
- Cleansing of dust and debris from hardware components
- Replacement of worn-out components before they fail
2. Reactive Maintenance
Also known as corrective maintenance, this type is performed in response to an issue that has occurred. While it's necessary to tackle unexpected failures, relying solely on reactive maintenance can lead to:
- Increased downtime
- Higher repair costs
- Possible damage to other connected equipment
Key Benefits of Regular PLC Maintenance
The advantages of implementing a consistent PLC maintenance program extend beyond immediate operational gains:
- Cost Savings: By investing in regular maintenance, businesses can minimize extensive repair costs and lessen the likelihood of costly downtime.
- Data Integrity: Well-functioning PLCs ensure that the data they capture and process remain accurate, supporting better decision-making.
- Regulatory Compliance: Many industries require adherence to safety and operational standards, which regular maintenance supports.
Choosing the Right Electronic Components Distributor in Canada
Partnering with the right distributor is pivotal to ensuring that you can access quality PLC components when needed. As an electronic components distributor in Canada, QF Automation stands out due to their commitment to customer satisfaction, extensive product selection, and expertise.
Why Choose QF Automation?
QF Automation offers several benefits, including:
- Wide Range of Products: They provide an impressive selection of electronic components essential for any automation system.
- Expert Technical Support: Their team is well-trained and can assist customers in troubleshooting issues and providing tailored solutions.
- Competitive Pricing: QF Automation offers fair pricing, which helps businesses manage their budgets efficiently.
- Timely Delivery: Understanding the urgency of your needs, they ensure fast shipping and local distribution across Canada.
Professional PLC Repair Services
Even with the best maintenance practices, PLC failures can occur. It's essential to have access to professional PLC repair services when they do. Many advantages of professional repair services include:
- Expertise: Technicians possess the necessary training and experience to diagnose and resolve complex issues accurately.
- Use of Quality Components: Reputable services use original parts, ensuring the reliability and durability of repairs.
- Warranty on Services: Many providers offer warranty coverage, giving you peace of mind regarding their work.
Common PLC Issues That Require Maintenance and Repair
Understanding the common PLC-related issues can help in preventive maintenance and timely repairs:
- Communication Failures: Issues in communication with I/O devices may indicate wiring problems or configuration errors.
- Input/Output Malfunctions: Faulty sensors or actuators can affect the entire control process. Regular checks can identify early signs of trouble.
- Power Supply Problems: Inconsistencies in power supply can compromise performance, often requiring immediate attention.
- Overheating: Excessive heat can damage components internally, necessitating checks on cooling systems.
How to Implement an Effective PLC Maintenance Program
To maximize the benefits of PLC maintenance, consider the following steps:
1. Assess Your Current Maintenance Strategy
Evaluate your existing processes and identify any gaps or weaknesses. This can include reviewing maintenance logs, downtime records, and maintenance costs.
2. Create a Maintenance Schedule
Develop a detailed maintenance schedule that outlines tasks and assigns responsibility. This should include preventive maintenance tasks and intervals.
3. Train Your Team
Ensure that your maintenance team is well-trained in PLC operations and maintenance techniques. Proper knowledge empowers them to quickly identify and rectify issues.
4. Utilize Technology
Consider employing maintenance management software to track work orders, schedule inspections, and log maintenance activities. Technology can streamline the process and provide data for analysis.
5. Partner with the Right Experts
A strong partnership with an electronic components distributor, like QF Automation, ensures you have access to quality resources for both maintenance and repair requirements.
Final Thoughts: Invest in Your PLCs for a Bright Future
Investing in a robust PLC maintenance program is an essential component of operational success in any industry reliant on automation. By maintaining PLCs, managing equipment life, and partnering with expert suppliers like QF Automation, businesses can achieve improved systemic efficiency and reliability.
Embrace the importance of proactive measures today, and watch your operational performance soar to new heights, ensuring that every facet of your automation remains exceptional.