Understanding Die Casting in the Automotive Industry
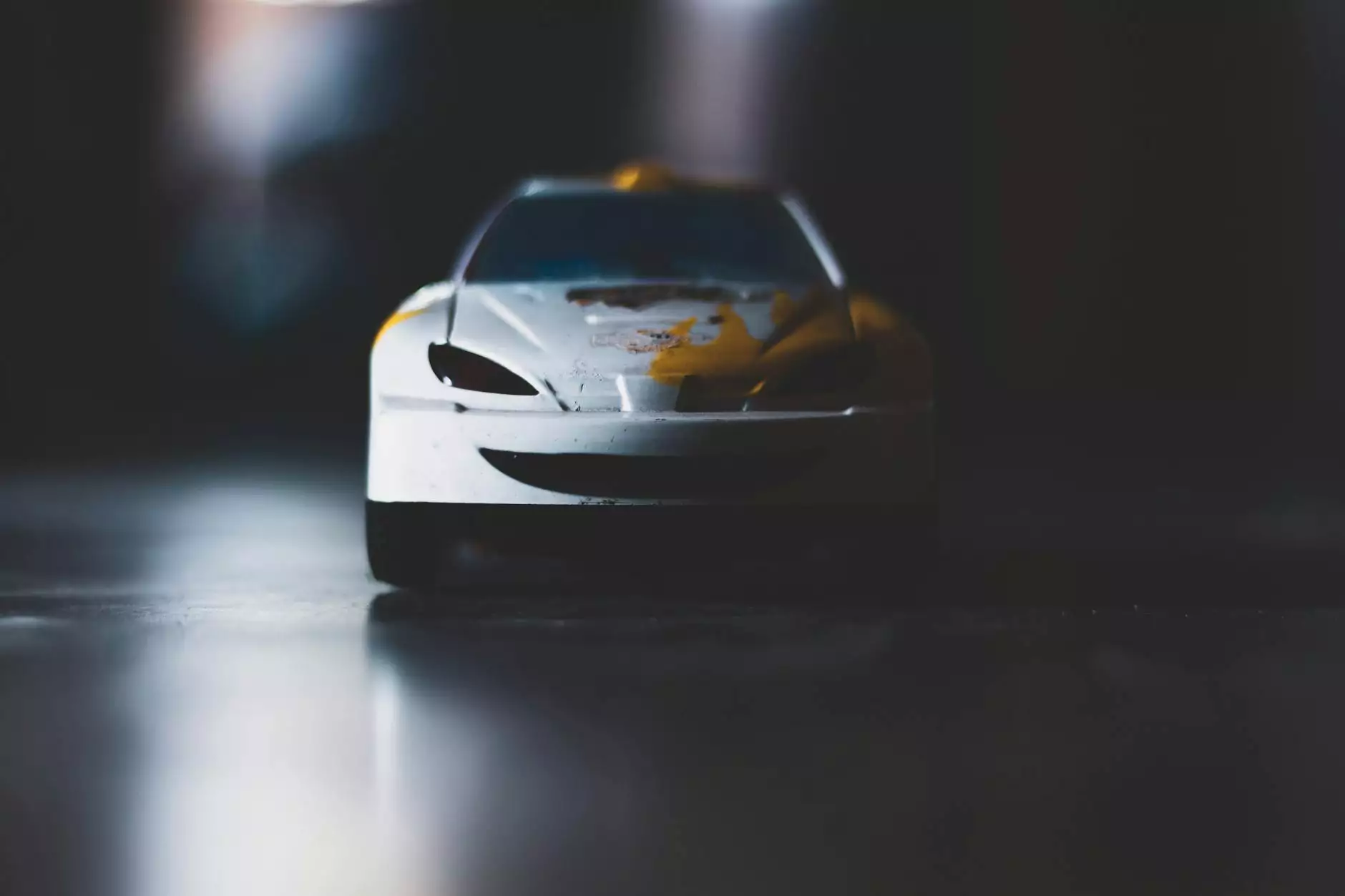
Die casting automotive components are essential in creating high-quality, durable, and efficient vehicles. The die casting process allows manufacturers to produce precise metal parts that fulfill the ever-increasing demands of the automotive market. This comprehensive guide will delve into the significance of die casting in the automotive industry, discussing its benefits, processes, and future trends.
What is Die Casting?
Die casting is a metal casting process that involves forcing molten metal into a mold cavity under high pressure. This technique is known for producing intricate shapes and forms with fine details, making it particularly advantageous in the automotive sector. The die casting automotive process typically involves two types of metals:
- Aluminum: Widely used due to its lightweight properties, which contribute to fuel efficiency.
- Zinc: Valued for its strength and durability, commonly used for smaller automotive parts.
Benefits of Die Casting in Automotive Manufacturing
Die casting offers several advantages that make it a preferred choice for automotive manufacturers. Here are some key benefits:
1. Precision and Complexity
One of the primary benefits of die casting is its ability to create highly precise parts with complex geometries. This precision reduces the need for additional machining and minimizes the potential for errors during assembly.
2. Cost-effectiveness
Although the initial setup cost for die casting may be high, the efficiency gained during mass production significantly reduces the cost per part. This makes die casting an ideal solution for producing high volumes of automotive components.
3. Lightweight Components
With the growing emphasis on fuel efficiency in the automotive industry, the use of lightweight materials is crucial. Die casting automotive parts, particularly those made from aluminum, help achieve significant weight reductions without compromising strength or durability.
4. Enhanced Strength and Durability
Die cast parts exhibit excellent mechanical properties, making them highly resistant to wear, corrosion, and fatigue. This durability translates to longer lifespans for automotive components, which is vital for the reputation and performance of any vehicle.
5. Streamlined Production Processes
The automated nature of die casting processes ensures faster cycle times and increased productivity. This efficiency translates into shorter lead times for manufacturers and quicker delivery of vehicles to market.
Key Die Casting Processes in Automotive Applications
There are two primary die casting methods employed in automotive manufacturing: hot chamber and cold chamber die casting. Each has its own specific applications and advantages.
1. Hot Chamber Die Casting
In hot chamber die casting, the molten metal is drawn from a furnace and injected into a die using a piston. This method is effective for metals with low melting points, such as zinc and magnesium, and is characterized by:
- Faster cycle times
- Reduced operational costs
- High production rates
2. Cold Chamber Die Casting
The cold chamber die casting process is employed for metals that have a higher melting point, like aluminum. In this process, the molten metal is poured into the chamber before injection. Benefits include:
- Compatibility with high-temperature alloys
- Greater design flexibility
- High dimensional accuracy
Applications of Die Casting in the Automotive Industry
The applications of die casting automotive processes are vast and varied. Here are several key components produced using die casting:
- Engine Blocks: Aluminum die casting is commonly used for engine blocks to enhance heat dissipation and reduce weight.
- Transmission Cases: These parts benefit from die casting's ability to create complex shapes while ensuring strength and durability.
- Suspension Components: Components like control arms are often produced with die casting due to their stress-bearing nature.
- Fuel Injection Housings: The intricate designs of fuel injection components suit the precision of die casting technology.
- Heat Exchangers: Die casting allows for the creation of effective cooling solutions through detailed geometric shapes.
Challenges Facing Die Casting in the Automotive Industry
Despite its numerous advantages, the die casting process is not without challenges:
1. Tooling Costs
The initial investment in the tooling required for die casting can be significant. However, this cost is offset by the long-term savings achieved through mass production.
2. Design Limitations
While die casting allows for complex shapes, certain design constraints must be considered, particularly when it comes to wall thickness and draft angles.
3. Quality Control Issues
Maintaining quality during high-volume production can be challenging. Manufacturers must implement rigorous quality control measures to ensure that every component meets the required standards.
The Future of Die Casting in the Automotive Sector
The automotive industry is evolving rapidly, and die casting automotive processes are adapting to meet these changes. Here are some emerging trends:
1. Increased Use of Electric Vehicles (EVs)
As the push for electric vehicles accelerates, the demand for lightweight and efficient components grows. Die casting will play a crucial role in producing parts that help enhance the performance and range of EVs.
2. Innovations in Materials
Research into new alloys and materials that can be used in die casting is ongoing. Innovations may lead to improved properties such as better heat resistance and increased strength.
3. 3D Printing in Tooling
The integration of 3D printing technology in creating die casting molds is on the rise. This hybrid approach can significantly reduce lead times for tooling and open up new design possibilities.
4. Sustainability Efforts
The automotive industry's focus on sustainability is prompting manufacturers to seek greener die casting practices, including the recycling of scrap materials and energy-efficient production methods.
Conclusion
Die casting has established itself as a cornerstone of the automotive manufacturing sector, delivering precision, efficiency, and durability. Understanding the die casting automotive landscape is vital for manufacturers aiming to stay competitive in a rapidly changing market. As the industry continues to evolve, the role of die casting will likely expand, further solidifying its place as a pivotal process in the production of high-quality automotive components.
For more information on how die casting can benefit your automotive manufacturing processes, consider exploring the expert services offered by deepmould.net.