Comprehensive Guide to OSHA H2S Training: Ensuring Safety and Compliance
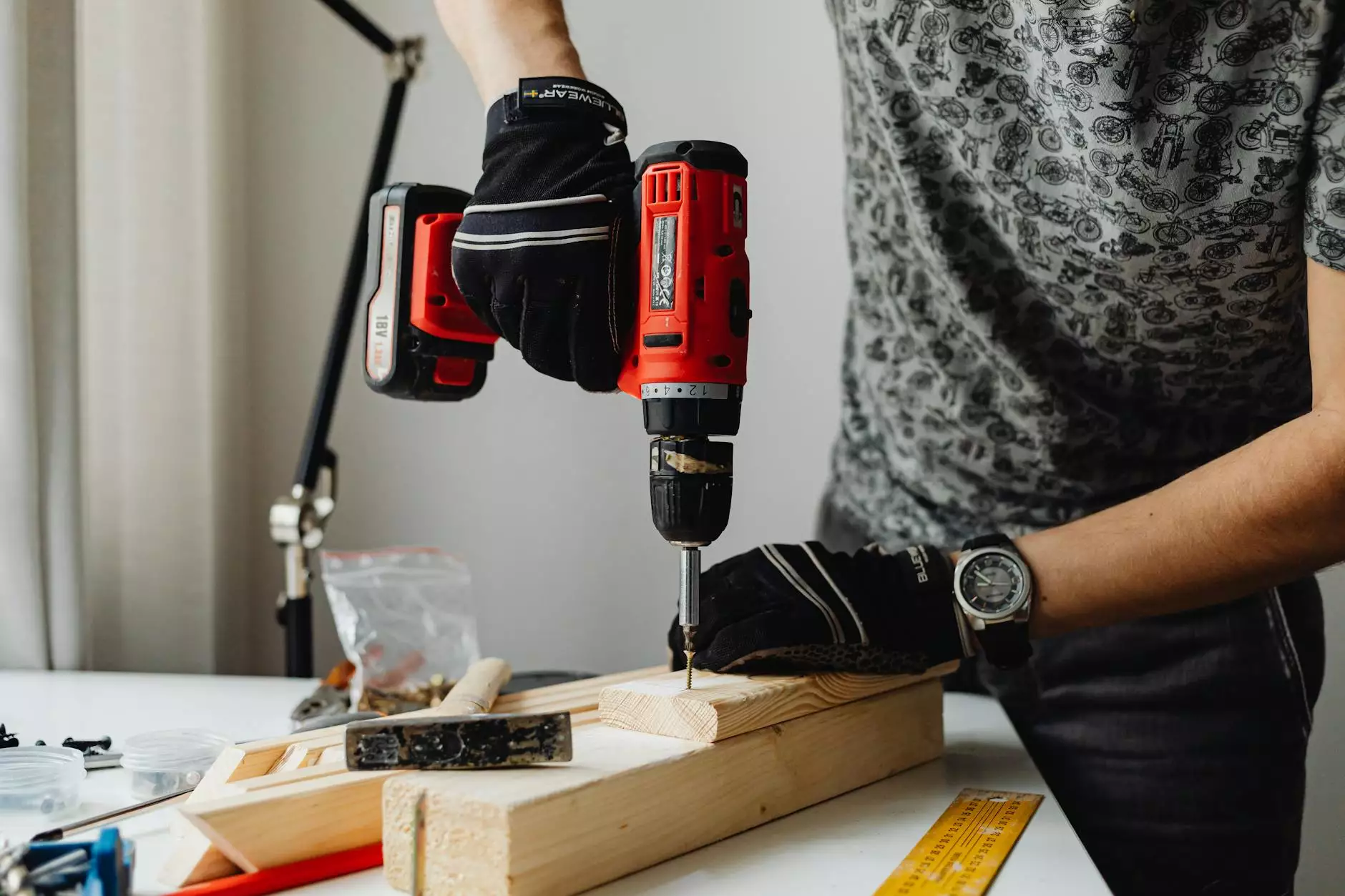
In today’s fast-paced industrial landscape, safety is paramount, especially in environments where hydrogen sulfide (H2S) is present. This sulfur-containing compound, often found in oil and gas drilling, sewage treatment, and other industrial settings, poses significant risks to health and safety. OSHA H2S training is crucial for educating workers about these hazards and ensuring compliance with federal safety regulations. This article will delve deep into OSHA H2S training, its relevance for businesses, and best practices for implementation.
Understanding Hydrogen Sulfide (H2S)
Hydrogen sulfide is a colorless gas known for its distinct rotten egg odor. While detectable at low concentrations, H2S can be deadly at higher levels. According to OSHA, exposure to H2S can lead to severe health complications, including:
- Respiratory distress
- Nausea and headaches
- Loss of consciousness
- Death in extreme cases
Given its hazardous nature, it is essential for workers in relevant industries to understand both the risks and safety procedures associated with H2S exposure.
The Importance of OSHA H2S Training
OSHA (Occupational Safety and Health Administration) sets forth regulations that require employers to provide necessary training to their employees. OSHA H2S training is integral for several reasons:
1. Enhancing Worker Safety
The primary purpose of OSHA H2S training is to equip workers with knowledge about the dangers of H2S and the necessary precautions to take. The training covers:
- Identification of H2S risks
- Emergency response procedures
- Use of personal protective equipment (PPE)
- Evacuation plans
2. Ensuring Legal Compliance
Businesses are legally required to adhere to OSHA standards. Failure to provide adequate training can lead to severe legal ramifications, including fines and penalties. By implementing OSHA H2S training, companies ensure they meet federal requirements, allowing them to avoid potential legal issues.
3. Fostering a Safety Culture
Training emphasizes the value of safety within the workplace. When workers are educated about potential hazards and the importance of safety measures, it promotes a culture of safety where employees feel responsible for their well-being and that of their colleagues. This cultural shift can lead to:
- Increased employee morale
- Reduction in workplace accidents
- Enhanced productivity
Key Components of an Effective OSHA H2S Training Program
An effective OSHA H2S training program should encompass several key components to ensure comprehensive employee education:
1. Awareness of H2S
Training should begin with a thorough overview of H2S, including its properties, sources, and health effects. Understanding H2S is the first step towards effectively managing risks.
2. Risk Assessment
Educating employees on how to assess their work environment for H2S risks is crucial. Training should include:
- Recognizing H2S release sources
- Using detection equipment
- Evaluating environmental conditions
3. Protective Measures
Workers must learn about the different types of personal protective equipment (PPE) necessary to protect against H2S exposure, which includes:
- Respirators
- Gas masks
- Protective clothing
4. Emergency Response Training
In the event of an H2S release, having a well-prepared emergency response plan is critical. Training should include:
- Evacuation procedures
- First aid for H2S exposure
- Use of emergency equipment
Implementing OSHA H2S Training in Your Business
When looking to implement an OSHA H2S training program, consider the following steps:
1. Assess Training Needs
Identify employees who work in high-risk areas or with H2S exposure. Tailor training to the specific needs and conditions of your work environment.
2. Choose a Certified Trainer
Ensure that the training is conducted by someone with expertise in H2S safety and compliance. Certified trainers can provide valuable insights and up-to-date information regarding OSHA regulations.
3. Use Interactive Training Methods
Engage employees by using hands-on training techniques such as:
- Scenario-based simulations
- Group discussions
- Interactive quizzes
4. Regularly Update Training
Safety regulations and best practices regarding H2S exposure can change. Schedule regular refresher courses to keep employees informed and trained on the latest safety measures. This also includes ongoing assessments of workplace safety practices.
Measuring the Effectiveness of Your H2S Training Program
It is essential to evaluate how effective your OSHA H2S training program is. Consider these metrics:
1. Employee Feedback
Gather feedback from participants through surveys or interviews to understand their perspectives on the training's effectiveness and areas for improvements.
2. Incident Reports
Monitor workplace incident reports for H2S-related issues. A reduction in incidents post-training can indicate a successful program.
3. Knowledge Assessments
Conduct assessments or tests after training to evaluate employees’ understanding of the material covered. This will help identify areas where further education is needed.
Conclusion
OSHA H2S training is not just a regulatory requirement; it is a critical investment in your employees’ safety and well-being. By implementing a robust training program, businesses not only comply with the law but also cultivate a culture of safety that can lead to higher employee morale, reduced accidents, and improved overall productivity. Remember, safety is everyone's responsibility, and every training session is a step towards a safer workplace.
For more information about OSHA H2S training and to explore comprehensive training solutions, visit h2sonlinetraining.com. Prioritize safety, ensure compliance, and pave the way for a safer work environment.