The Evolution and Importance of Automotive Molds in the Metal Fabrication Industry
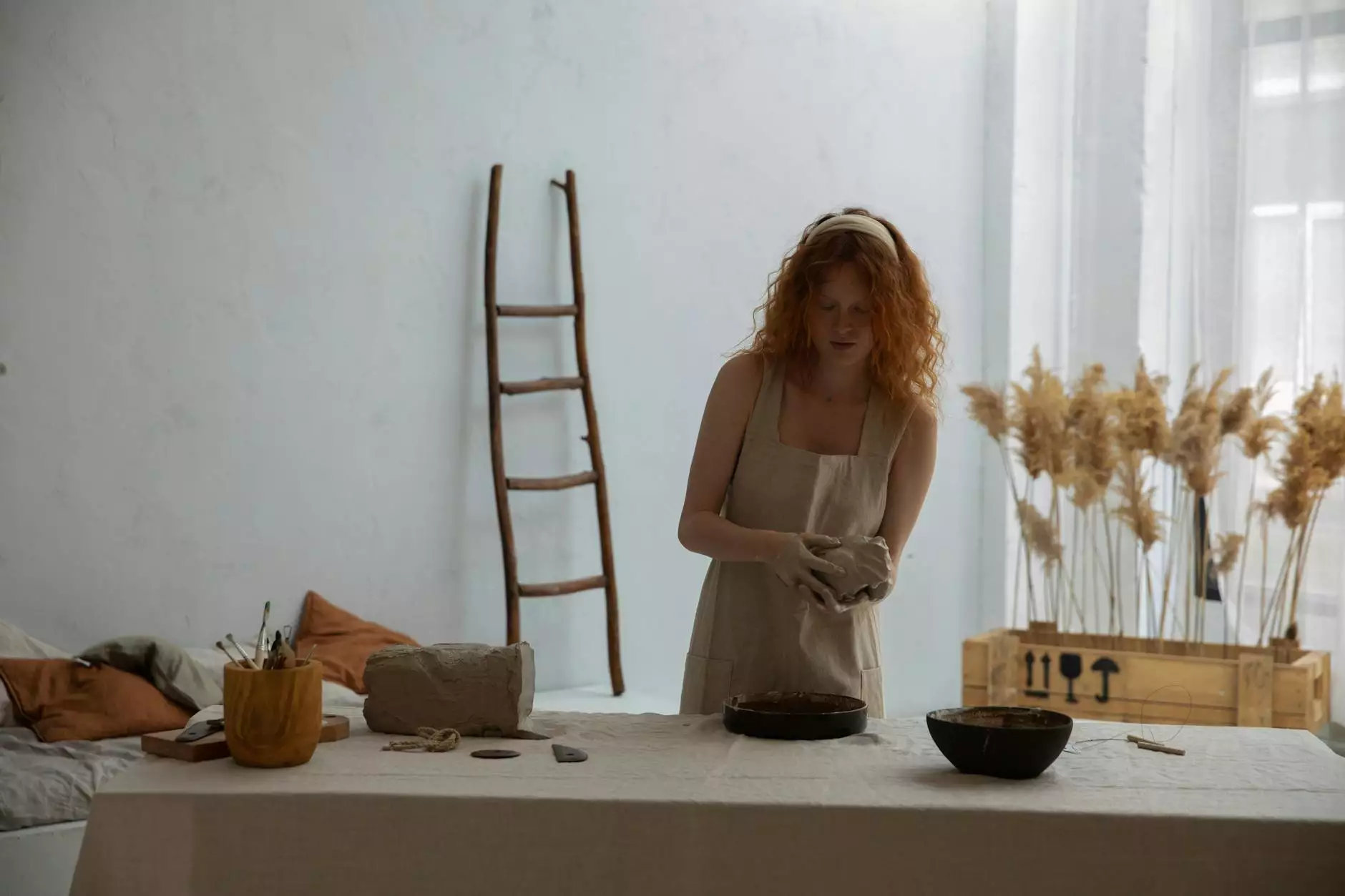
The automotive industry is a rapidly evolving sector that requires continuous innovation and development. At the heart of this evolution are automotive molds, which play a crucial role in the production of a wide range of automotive components. In this comprehensive article, we will explore the significance of automotive molds, the processes involved in their creation, and how they contribute to the overall efficiency and quality within the automotive manufacturing domain.
Understanding Automotive Molds
Automotive molds are essential tools used in the shaping and manufacturing of various automotive parts. These molds are designed to accommodate the specific requirements of complex automotive designs, enabling manufacturers to produce high-quality components with precision. The process of creating automotive molds involves several stages:
- Design and Prototyping: This initial stage involves the creation of a detailed mold design using Computer-Aided Design (CAD) software. Prototyping helps to verify the mold's practicality before actual production begins.
- Material Selection: The choice of materials is crucial for the durability and performance of the mold. Common materials include steel and aluminum, known for their strength and resistance to wear.
- Manufacturing: The molding process itself can involve various techniques, including injection molding, compression molding, and blow molding, each suitable for different types of components.
- Testing and Quality Assurance: After production, molds undergo rigorous testing to ensure they meet industry standards and specifications.
The Role of Automotive Molds in Metal Fabrication
In the metal fabrication sector, automotive molds serve as a bridge between design and reality. They enable manufacturers to translate complex designs into tangible products efficiently. The integration of automotive molds into the manufacturing process provides several benefits:
- Enhanced Precision: With the use of advanced technologies, automotive molds produce consistently precise components, reducing errors and minimizing waste.
- Increased Production Speed: Automation in the molding process allows for faster production cycles, which is critical in meeting market demands.
- Cost Efficiency: While the initial cost of creating molds can be high, they significantly reduce the cost per unit in mass production.
- Flexibility: Modern molds can be designed to produce a variety of components, making them adaptable to changing automotive designs and technologies.
Innovations in Automotive Mold Technology
As the automotive industry progresses, so too does the technology surrounding automotive molds. Recent innovations have pushed the boundaries of what is possible, enhancing both the quality and efficiency of the molding process. Some noteworthy advancements include:
1. 3D Printing
3D printing technology has revolutionized mold-making by allowing for rapid prototyping and the production of complex geometries that were previously unattainable with traditional methods. This technology significantly reduces lead times and allows manufacturers to test new designs quickly.
2. Advanced Materials
New materials, such as high-performance polymers and composites, are being used in mold production, which enhances the durability and thermal stability of molds, thus increasing their lifespan and reducing maintenance costs.
3. Smart Manufacturing
Integrating Internet of Things (IoT) technology into the molding process provides real-time data analytics, which helps in predictive maintenance and improving overall production efficiency.
Applications of Automotive Molds in the Industry
Automotive molds are utilized in the production of various automotive components, ranging from interior parts to structural elements. Some of the most common applications include:
- Dashboard Components: Molds are used to create complex dashboard designs that enhance aesthetics and user experience.
- Exterior Panels: Automotive molds facilitate the production of body panels, ensuring precision in fit and finish.
- Fluid Reservoirs: Molds for producing components like fuel tanks and coolant reservoirs are vital for the vehicle's performance.
- Electrical Housings: The production of housings for electrical components requires precise molding to ensure safety and functionality.
Challenges in Automotive Mold Manufacturing
Despite the numerous advantages, the manufacturing of automotive molds does come with its challenges. Understanding these obstacles is crucial for manufacturers to develop effective strategies to overcome them:
1. High Initial Costs
The initial investment for designing and constructing molds can be significant, making it imperative for manufacturers to find ways to optimize their production processes.
2. Design Complexity
As automotive designs become more intricate, creating molds that can accommodate these complex shapes requires advanced engineering and innovative solutions.
3. Material Limitations
While new materials are continuously being developed, selecting the right material for a specific application remains a critical challenge, particularly for parts subject to high stress or extreme temperatures.
The Future of Automotive Molds in the Industry
The future of automotive molds looks promising as the industry continues to adapt to new technologies and methodologies. The ongoing shift towards electric vehicles (EVs) and autonomous driving systems is likely to create new demands and opportunities for mold manufacturers. For instance:
- Focus on Lightweight Materials: With the push for fuel efficiency and performance, mold manufacturers are likely to explore more lightweight materials that can be shaped into new component designs.
- Increased Customization: As consumers demand more personalized vehicles, the ability to quickly adapt molds for custom parts will become essential.
- Sustainability Initiatives: There will be a greater emphasis on sustainable practices, including the use of recyclable materials and eco-friendly manufacturing processes.
Choosing the Right Partner for Automotive Molds
As a business in the automotive sector, partnering with a reliable and proficient manufacturer of automotive molds is paramount. At Deep Mould, we specialize in delivering high-quality molds tailored to your specific needs. Here are key considerations when selecting your mold manufacturing partner:
- Experience and Expertise: Look for a company with a proven track record in molding technology and automotive applications.
- Technological Capabilities: Ensure they utilize advanced technologies like CAD, CAM, and 3D printing.
- Quality Assurance Processes: Investigate their quality assurance protocols to guarantee mold durability and reliability.
- Customer Support: Choose a partner who offers robust customer support and collaboration throughout the design and production process.
Conclusion
In conclusion, automotive molds are a fundamental element in the metal fabrication industry, directly impacting the quality and efficiency of automotive production. As technology continues to innovate and the industry evolves, the importance of high-quality molds will only increase. By understanding the processes, benefits, and future trends of automotive molds, businesses can position themselves to thrive in this competitive landscape.
At Deep Mould, we are committed to providing exceptional solutions in automotive molds that meet the high standards of today’s automotive challenges. Contact us today to discover how we can help you succeed in your endeavors!